Teachers use 3D printers to make change
The 3D printers from Homestead are being used to make respiratory device parts.
As coronavirus continues to make an impact on the nation, and the world, many civilians are rallying together and showing just how much humanity can do for each other. After schools closed on March 13 for the Mequon Thiensville School District (MTSD), and many schools in the surrounding area, Mr. Joe Ciurlik, social studies and AVID teacher, and Mr. Jeff Patterson, science teacher, knew they had to help.
With five 3D printers sitting idle at Homestead, Ciurlik and Patterson knew they could be put to good use during this time. “I saw the need,” Ciurlik said. “I saw a bunch of stuff out on social media, so I emailed Mr. Patterson and said ‘Hey we have 3D printers at school, let’s use them’.” This idea however, could not be put into play immediately.
As soon as Ciurlik and Patterson had decided to move the printers to Ciurlik’s basement, the stay at home order was put into place in Wisconsin. This meant all faculty and personnel were no longer able to enter the building at Homestead. Ciurlik and Patterson did not stop there.
“About a week or two later Ms. Croix, the director for technology services for the district, sent me an email about an email she had received from Concordia University asking if there were some districts in the area with 3D printers and if they would be willing to print masks,” Patterson said. Patterson got in contact with Ciurlik again, and they decided to continue the plan they had initially thought of.
Eventually teachers were allowed in Homestead on designated staff pick up days and they were able to collect the printers and transfer them to Ciurlik’s house.
They began using the 3D printers to print specific parts for masks on respiratory devices in hospitals. “So we print the body for the mask and the filter. What they do at Concordia is they take layers of material to provide a filter and put the mask together,” Patterson said. Once Concordia assembles the masks they are shipped to local hospitals, EMT’s and first responders to be used on the frontlines of COVID-19.
As for printing the mask, each one takes about ten hours to print, and Ciurlik has the printers running 24/7 in his basement. Ciurlik wakes up at 4:30 a.m. everyday to switch out the masks and begin printing new ones. He says it has become a family affair in his household. Collectively, they have produced almost 150 masks so far.
With school now being cancelled for the rest of the year, Ciurlik and Patterson plan on continuing to produce masks with the 3D printers for as long as they can. “Change always comes from people who are committed to changing the world. It’s just the way I was raised, and if you can help out, you should,” Ciurlik said.
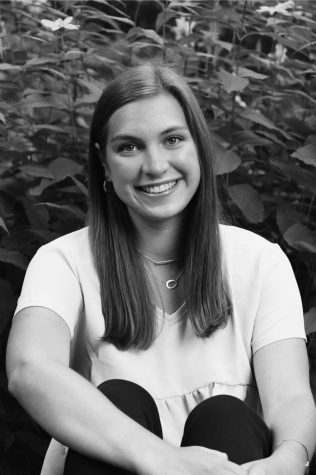
Hannah Kennedy is a senior at Homestead and serves as editor in chief of Highlander Publications. She is going to study journalism in college at the University...